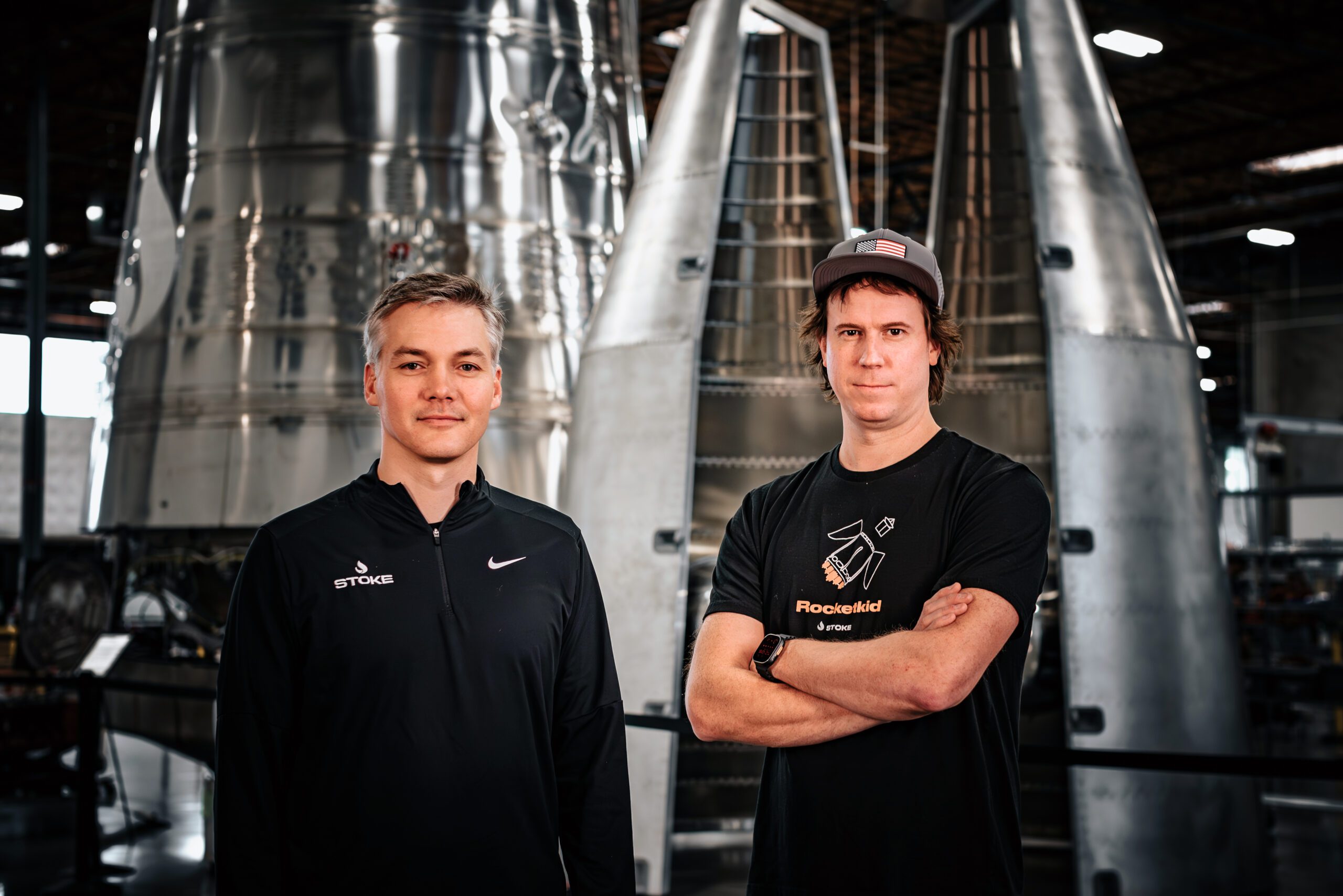
The future of spaceflight, and why we built Stoke
By Andy Lapsa, CEO and co-founder of Stoke
When Tom Feldman and I founded Stoke in 2019, there were already something like 150 rocket startups. On the surface, the last thing the world needed was company number 151.
But then we did the math.
What we found gave us enormous conviction that 1) the future of space will be defined by fully and rapidly reusable rockets that operate with aircraft-like frequency, and 2) the time to build them is now. Five years later, that conviction has only deepened. The partially reusable rockets of today are an important stepping stone, but they are not the destination. Any launch system that wasn’t designed from the outset for full and rapid reuse will soon be left behind.
Surprisingly, we couldn’t find another startup building a credible path to this future.
Somebody had to do it, so why not us?
The economics of rapid reusability
There are two primary cost drivers in space launch:
- The cost to manufacture the rocket
- The fixed cost of everything else — factories, test facilities, launch complexes, labor, etc.
The first is intuitive. Rockets are multi-million-dollar precision machines built to contain some of the highest sustained energy densities produced by humans (second only to certain nuclear devices). These are not paper cups, and it makes no sense to throw them away after a single use.
The second driver — the cost of everything else — is less visible but just as critical. Regardless of whether you build one rocket or one hundred, you need the same core infrastructure. These fixed costs often add up to billions of dollars that are rarely acknowledged in the headlines, which typically focus on marginal cost alone. But in any real business, fixed costs can’t be ignored.
The economics work like this: Each launch helps amortize the cost of infrastructure. If you launch once, that launch bears the full burden. Launch a thousand times, and each launch only has to contribute 0.1%.
This is why flight frequency is almost as important as reusability itself. A 2016 U.S. Air Force study modeled this relationship and found that, with full reusability and a high flight cadence, launch costs can be reduced from today’s multi-thousand dollars per kilogram to just a few hundred (see Figure 1). And this isn’t a theoretical promise — air travel proves it daily. A Boeing 737 costs more to produce than a Falcon 9, but the 737 moves passengers and cargo anywhere in the world for under $3 per kilogram.
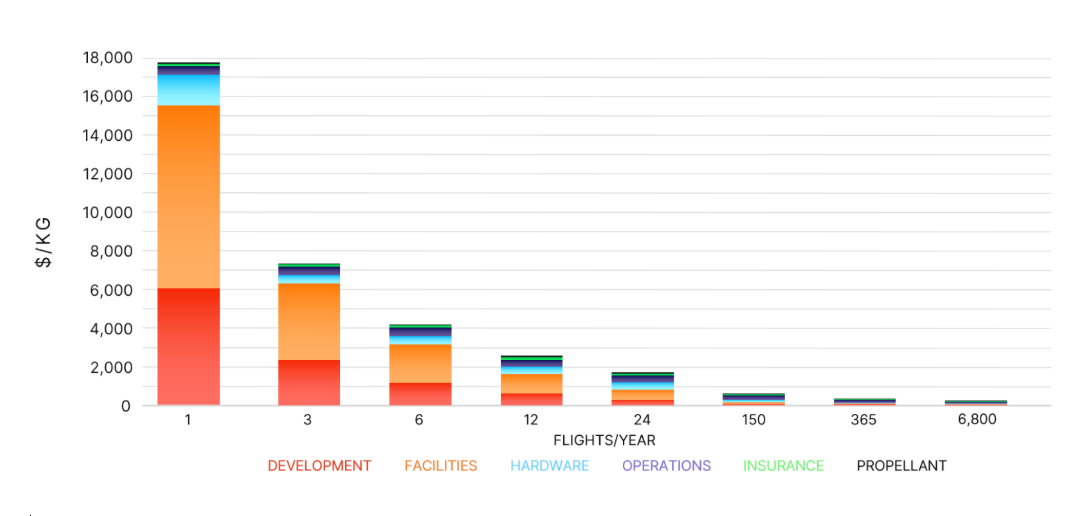
Given its importance to the cost economics, flight frequency deserves just as much attention as reusability. Yet historically, launch frequency has been hard to scale. More launches have meant that more rockets, more/bigger factories, more test facilities, more staff, and more fixed costs would be required. That’s why, as shown in Figure 2, no company has been able to launch more than 20 times per year without first achieving at least partial reusability — even at the micro-launcher scale.
This is where reusability becomes transformational. It’s not just about recouping hardware costs; it’s about enabling higher launch rates without scaling up infrastructure. That’s how SpaceX has increased flight cadence while others have plateaued.
But even that system has limits. Each Falcon 9 launch still requires a new second stage (which means a new structure, new engine, new fluid systems, new avionics, and one-off test verifications of all of the above). Second-stage production and verification are now Falcon 9’s flight-rate limiter. The only way to keep scaling — and keep costs dropping — is to reuse the entire vehicle.
That’s never been done before, but it’s time.
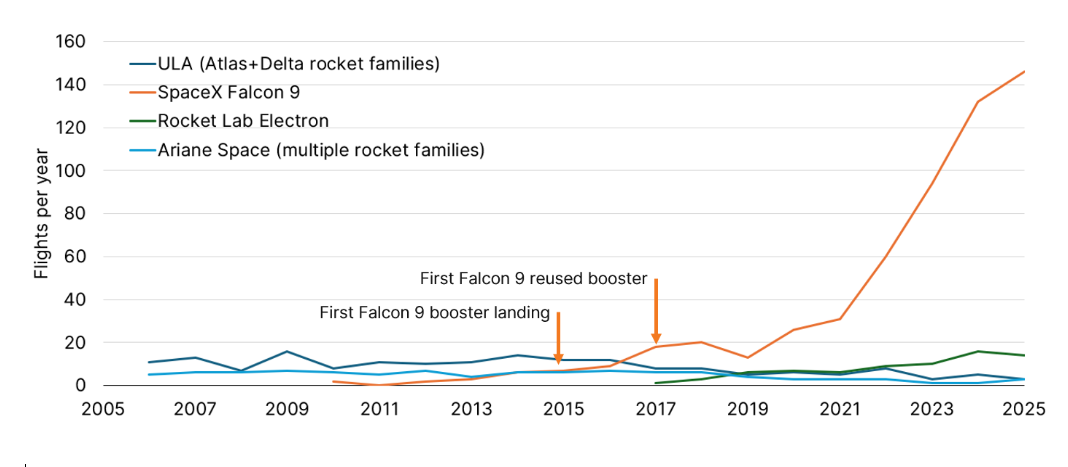
Cost, availability, and reliability: A virtuous cycle
Three things matter most to customers of any transportation system: cost, availability, and reliability.
For decades the cost of launch has been the major barrier, but availability isn’t far behind. Current lead times for launch are 18 months or more. Even then, available destinations are limited. Imagine trying to conduct business — or even sending packages at the holidays — with those conditions. Most people wouldn’t do it. In that situation, transportation only makes sense for a small number of use cases.
Full reusability changes that. Higher flight rates not only lower costs but also create more availability for customers. It’s a win-win that is impossible to ignore.
And the benefits go even deeper.
Reusability also fundamentally changes the drivers of reliability, another area where our industry has struggled. Figure 3 shows the result of every launch worldwide since 1957. Despite decades of progress, failure rates remain persistent; in each year since 1980, between 2% and 8% of orbital launch attempts failed to reach their intended orbit.
Perfection in scaled manufacturing is very hard to achieve, regardless of the industry. That’s why automotive lemon laws exist. That’s why aircraft go through extensive flight acceptance test protocols before being placed into service. And that’s why flight-proven reusable rockets will change the fundamentals of reliability in our industry.
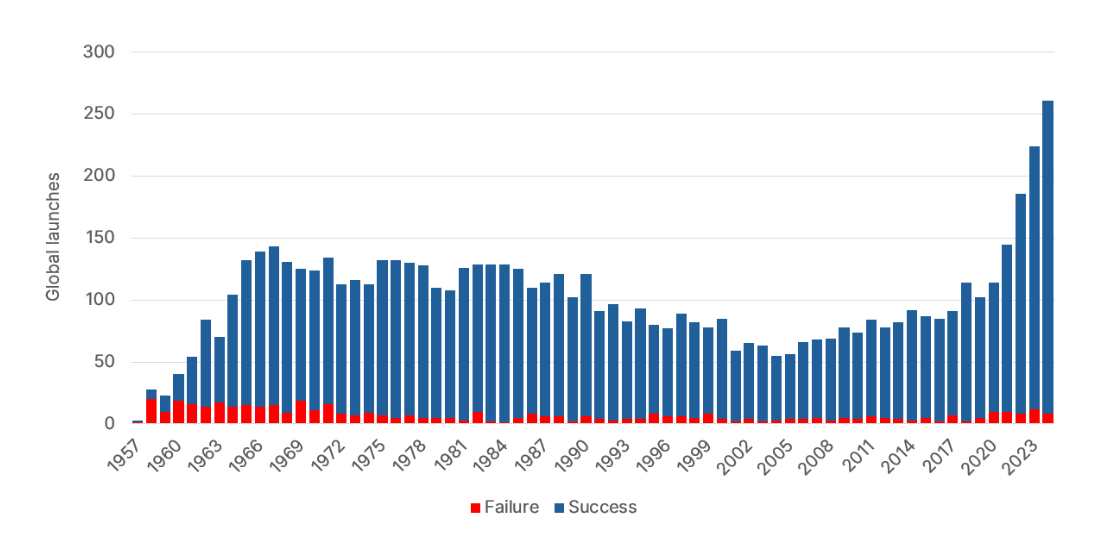
In fact, we’re already seeing this play out. SpaceX is the gold standard in launch today, with an industry-leading combination of reliability and flight cadence. Out of the past 300 Falcon 9 launches, only three have failed to achieve their mission. Every one of those failures was due to a malfunction of the disposable second stage, the part of the rocket making its maiden voyage on every flight. The reusable first stage has a perfect record of success in that span.1 If the same is achieved with the second stage, spaceflight becomes dramatically more reliable.
Full and rapid reuse is therefore the key to solving all three core challenges of space transportation:
- It reduces cost,
- It increases availability, and
- It enhances reliability.
And the better you are at one, the better you’ll be at the others. If space is to become a truly scalable economy, it’s impossible to believe that there will be any other end state.
The time is now
As a civilization, we’ve been launching rockets for over 70 years. Until recently, however, there was little incentive to reduce launch costs. Historically, most missions were used for multi-billion-dollar government-funded projects where the $200 million launch cost was just a rounding error for the overall program.
Times have changed.
Thanks to the advances and miniaturization of modern electronics, satellites today are smaller, cheaper, and more numerous. Now, launch represents between 30% and 70% of the total cost of deployment for commercial satellite constellations. In most cases, it’s the single largest expense. This is why the economic incentive to reduce launch costs has never been stronger.
From Earth sensing to commercial GPS, global connectivity, life-saving drug manufacturing, sustainable energy production, and strategic national security capabilities, space is primed to be a major extension of the global economy. As with any market, though, it only works if there is healthy competition between multiple players in multiple verticals. This is why improved access to space is so important; lower launch costs, more availability, and better reliability lowers the barrier to entry for a wide range of new and important businesses.
Meanwhile, a new generation of engineers — unburdened by legacy thinking and trained to reason from first principles — is ready to build what’s next. Many of them have already cut their teeth on bringing revolutionary components, subsystems, and entire vehicles from cradle to grave. They understand what works through practical experience, and they have a vision for how things can be improved on their next attempt.
The technical foundation is there. The business case is clear. The talent is available. Now is the time to deliver on the long-promised future of spaceflight.
And that’s why we’re building Stoke.
1Several boosters failed to be recovered in that span, but none of them compromised the mission.